4 tendencias en pintura industrial
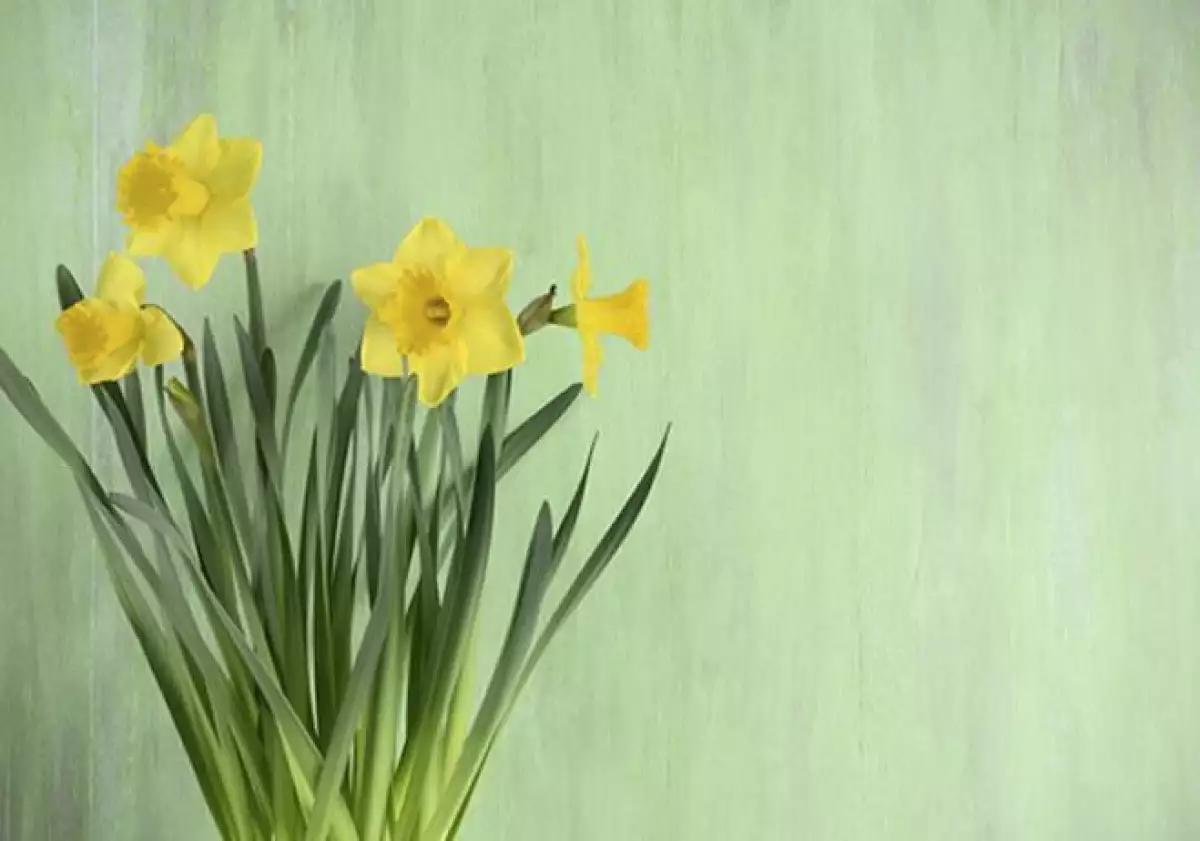
Ya sea la automoción, bienes de consumo, maquinaria y equipos, las comunicaciones, la electrónica, la arquitectura, la medicina o la energía, prácticamente no hay área industrial en la que la técnica de pintura no esté presente, señala un comunicado de PaintExpo.
La técnica de superficie y, por lo tanto la del lacado industrial, cada vez tiene mayores exigencias. Resultan decisivos los aspectos de la eficiencia de los recursos, la individualidad y la compatibilidad medioambiental. En el comunicado “Respuestas para una mayor demanda de recubrimiento” se indica que también juegan un papel importante las nuevas áreas de aplicación, la calidad y la flexibilidad.
Las superficies tienen que cumplir las más variadas exigencias funcionales y decorativas. Independientemente del material, a nivel mundial siempre se trata de que se pinte y se revista teniendo en cuenta al máximo el medio ambiente, la eficacia de recursos y la alta calidad.
Para alcanzar estos objetivos, se disponen de distintas propuestas y técnicas que atienden los desafíos de la industria actual.
Coil coating
Forma parte de soluciones nuevas y avanzadas a lo largo de las cadenas del proceso de pintura húmeda, pintura en polvo y Coil Coating. Por ejemplo, en el pre-tratamiento de sustratos metálicos cada vez se imponen más los fosfatados de hierro, que despliegan su efecto ya a una temperatura de entre 30°C a 35°C en lugar de hacerlo sólo de 40°C a 60°C, así como sistemas nano-cerámicos.
De acuerdo con PaintExpo, ahora ya están disponibles productos basados en materias primas renovables para el tratamiento previo y la limpieza de las piezas de acero, hierro y aluminio. Para el pre-tratamiento de las piezas de plástico van en aumento los métodos alternativos, como la limpieza por chorro de nieve y de plasma.
Revestimientos de función optimada
En el área de las lacas, la tendencia se dirige hacia sistemas que cumplen tanto requisitos decorativos como funcionales. Para pinturas y barnices con base de disolvente para el revestimiento de metales, materiales plásticos y madera, entre otros, también están disponibles aditivos que le dan a la pintura una propiedad antimicrobiana.
Se basa en materiales orgánicos de metal con efecto ionizante, prosigue el comunicado. Estas sustancias también se utilizan en recubrimientos en polvo recién desarrollados que tienen un efecto antimicrobiano. Cuando se trata de protección contra la corrosión, así como la resistencia de componentes contra UV y los efectos de la intemperie, por ejemplo, para maquinaria de la construcción, agrícola y el uso al aire libre, las exigencias han ido en aumento.
Éstas se pueden cumplir, de forma efectiva y respetando el medio ambiente, empleando una imprimación de pintura en polvo libre de zinc y metales pesados a base de epoxi. Cumple con los requisitos de protección contra la corrosión hasta la clase C5-I-lang y puede ser aplicada tanto con pintura en polvo como pintura líquida. La imprimación anticorrosiva se ofrece como solución óptima adaptada al sustrato a recubrir (metales ferrosos, sustratos con bordes afilados, piezas de fundición).
Otra solución de revestimiento en polvo de dos capas, de nuevo desarrollo para la protección anticorrosiva, permite un revestimiento sin las reticulaciones intermedias de alto consumo energético. La imprimación y la capa de acabado se aplican en la pieza por medio de la técnica Tribo de polvo sobre polvo y, a continuación, ambas capas se reticulan en una sola operación.
Avanza la tecnología UV
La importancia de la tecnología UV sigue creciendo tanto en el revestimiento de componentes de material de plástico como de metal, puesto que cada vez más se pueden revestir piezas más complejas con esta técnica.
El curado UV se lleva a cabo bajo una atmósfera de gas inerte, en el que por el uso de, por ejemplo, CO2 o nitrógeno, predomina una atmósfera reducida de oxígeno. Esto evita que los radicales necesarios para la polimerización reaccionen con el oxígeno en el aire y que haya una inhibición de oxígeno.
Se puede curar a mayores distancias y áreas que reciben significativamente menos radiación UV y endurecen mejor. Además de los tubos de descarga de gas, para el curado de barnices UV se emplean ahora también focos LED.
Nitrógeno
Bajo el aspecto de la eficiencia de materiales para la aplicación de solventes y pinturas a base de agua y 'High Solids', se están comprobando también gases atomizantes como alternativa. Ello, mediante el uso de nitrógeno, permite un ahorro de material de entre el 5% y el 45%.
Un método bien establecido en diversas aplicaciones de producción en serie en el campo de la automoción también permite ventajas en la calidad de la pintura, el rendimiento y la disponibilidad de las instalaciones.
La 5ª Feria líder del sector de técnicas de lacado industrial se llevará a cabo en Karlsruhe (Alemania) del l 8 al 11 de abril de 2014.