Zinag, la futura aleación indeformable de las industrias
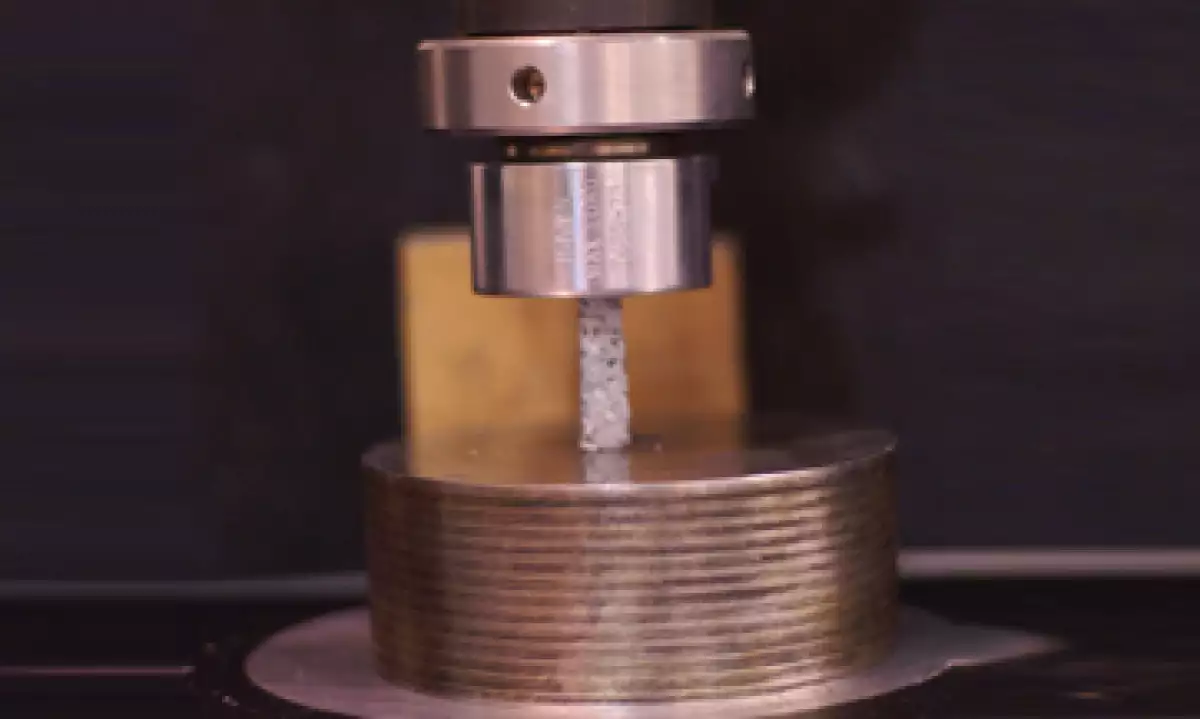
Su nombre es zinag y por ser una aleación de metales prácticamente indeformable, podría ser el material del futuro en la industria automotriz y muchas otras. Su creador: un científico mexicano.
El zinag es una aleación de zinc, plata y aluminio capaz de absorber impactos y estirarse hasta 1,000 veces su tamaño sin deformarse.
Las piezas fabricadas con zinag pueden ser remplazadas y usadas de nuevo; además de ser reparadas hasta en 10 ocasiones, explica el doctor en Ciencias de los Materiales por la Universidad Nacional Autónoma de México (UNAM), Said Robles, su inventor.
El desarrollo posee la característica de ser duro, ligero y con propiedades térmicas y mecánicas. A diferencia del acero, no sufre corrosión, y puede sustituir materiales escasos y de mayor costo como el titanio.
Robles explica que desarrolló una tecnología de absorción de impacto y energía que mejora la seguridad de los automóviles durante una colisión.
"El material se convierte en un elemento poroso, es decir, es una aleación donde la transformación tecnológica permite producir un lingote que se convierte en un material de baja densidad que absorbe el impacto y la energía. Esto hace que tenga más aplicaciones en el sector automotriz", dice el científico en entrevista con a Manufactura.mx.
Lee también: Toyota apuesta por vehículos antichoques
La aleación está compuesta por zinc, plata y aluminio. Foto: Said Robles/Cortesía
Además, el zinag ofrece reducción en tiempo y costo de fabricación de insumos en comparación con los materiales utilizados hoy en la manufactura automotriz como la lámina de alumino y la fibra de vidrio.
De acuerdo con Robles, el costo de producción del zinag puede ser hasta 60% más barato y puede variar de los 250 a 1,250 pesos por kilo según la porosidad y resistencia.
"Normalmente, en el uso de la lámina de aluminio las automotrices necesitan de una prensa hidráulica para darle forma a la carrocería, más el gasto de luz y el tiempo para que quede moldeado bajo los controles de calidad que tenga cada empresa. En el caso del metal foam los tiempos y costos se reducen al uso de menos equipo, pero con la misma calidad", indicó el doctor en Ciencia de los Materiales.
La aleación se utiliza de dos diferentes formas en un auto. La primera consiste en moldear el material en forma de una lámina súper plástica destinada a integrar la carrocería del vehículo.
En la segunda, la aleación es transformada en metal foam o espuma metálica, la cual se aplica en la zonas más expuestas a colisión como las salpicaderas, defensas o laterales.
La porosidad y la resistencia son elementos clave de la aleación. FOTO: Said Robles/Cortesía
Para producir el material, la aleación se somete a altas temperaturas y presión de aire, lo que al término le permite conservar sus propiedades.
El material fue aplicado en el auto experimental Inferno, un vehículo deportivo de patente mexicana, que puede alcanzar los 395 kilómetros por hora y fabricado por la empresa LTH Hot Sport. El vehículo registró una resistencia alta a los impactos.
Nota: Mexicanos diseñan auto indeformable
La aleación Zinag ya fue probada en el auto deportivo experimental Inferno .FOTO: LTH Hot Sport/Cortesía.
Robles Casolco dice que empresas automotrices, sin especificar cuáles, han tenido acercamiento con el desarrollo, que ya cuenta con un registro de propiedad intelectual impulsado por la UNAM y por el Instituto Tecnológico de Estudios Superiores de Monterrey.
El también académico de la Universidad Autónoma del Estado de Morelos (UAEM) señaló que el zinag puede utilizarse en otros sectores de la industria como construcción como material antisísmico, o armamentístico pues podría sustituir al kevlar de equipamiento policial o militar.