El nuevo empleo de la revolución 4.0
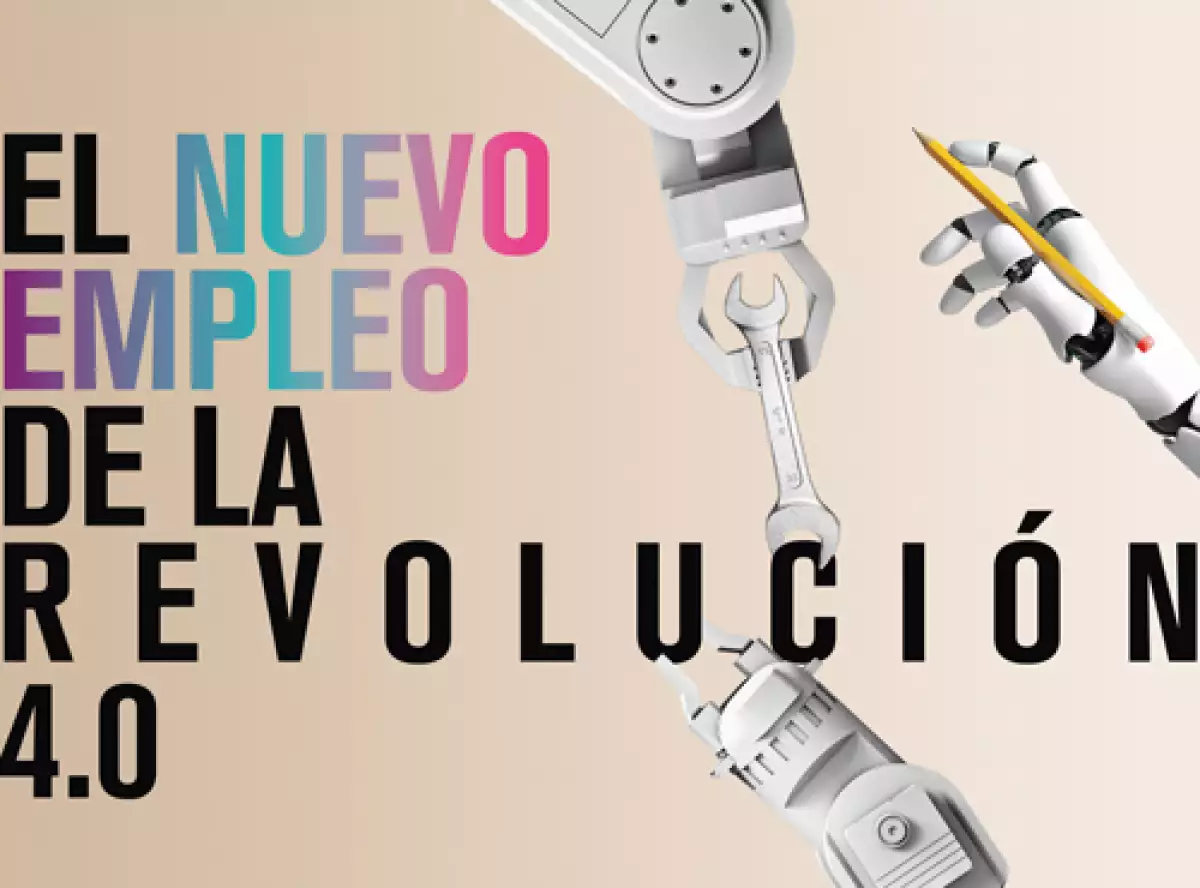
Nota del editor: El texto de este artículo fue publicado en la edición 265 de la revista Manufactura, Adiós al empleo como lo conocemos, correspondiente a febrero de 2018.
Una pieza se cuela en la fila y rebasa a la que tiene delante hasta la siguiente estación de la línea de producción, donde un robot le aplicará pintura. La otra, que se quedó rezagada, en realidad se someterá a un proceso diferente, pues el consumidor ha solicitado cierta personalización en el automóvil del que formará parte.
En esta zona no hay personas: toda la producción es llevada a cabo por robots, que son capaces de comunicarse con las piezas a través de sensores; el producto es capaz de notificar al sistema de producción qué tipo de proceso necesita. Es un ejemplo de la manufactura inteligente y no es una imagen del futuro: la revolución industrial 4.0 ya está en marcha.
Recomendamos: Conoce el arma eléctrica de Porsche
La Federación Internacional de Robótica (IFR, por sus siglas en inglés) estima que para 2020 habrá 3,053,000 millones de robots industriales en operación, 67% más que los 1,828,000 registrados en 2016. El crecimiento anual promedio entre 2018 y 2020 será de 14%, según las previsiones del organismo publicadas en septiembre de 2017.
México fue, en 2016, el octavo país del mundo que más robots industriales adquirió (5, 900 unidades), aunque los primeros cinco (China, Corea del Sur, Japón, Estados Unidos y Alemania) representan 74% del mercado, según los datos de IFR. El año pasado, el número de robots en operación en el país incrementó 10% respecto al año anterior y la previsión es que entre 2018 y 2020 lo haga a un ritmo de 11% anual.
Leer: México debe preparar a sus jóvenes para desarrollar la industria 4.0
Si los datos son fríos y no dan una magnitud del cambio en los procesos de producción, hay que visitar una fábrica de cualquier sector productivo para entenderlo. No se trata solo de ver robots donde antes circulaban montacargas dirigidos por personas.
La inteligencia artificial, el machine learning o el internet de las cosas han modificado las formas de producción, presionadas a su vez ante los menores ciclos de vida de los productos y la demanda de los consumidores por nuevas novedades.
Leer: La evolución 4.0 de la industria química y farmacéutica
Estos cambios también se trasladarán al ámbito laboral. El Foro Económico Mundial (WEF, por sus siglas en inglés) ya lo señaló a principios de 2016, en el estudio ‘El futuro del empleo’: 65% de los niños que comienzan ahora la primaria desempeñarán en su vida adulta un trabajo que actualmente no existe.
De acuerdo con el análisis, entre 2015 y 2020 se prevé que la automatización y digitalización suponga la pérdida de 7.1 millones de empleos, sobre todo administrativos. Pero la moneda tiene otra cara: la creación de dos millones de nuevas posiciones en áreas de computación, matemáticas e ingeniería.
Recomendamos: 3 carreras que hoy demanda la Industria 4.0
Sin embargo, las habilidades de los ingenieros dentro de 15 años distarán mucho de las de aquellos que salen actualmente de las aulas. El escenario que ha llevado a pensar que podría experimentarse una crisis en el empleo. “Hoy, no hay ningún indicador que diga que se está llevando a cabo una reducción de (puestos de) trabajo por los robots y la inteligencia artificial.
La productividad va creciendo y el paro en América Latina se reduce. El desempleo es más por la globalización que por la automatización. No hay un indicador de alarma hoy, pero eso no quiere decir que no lo haya en el futuro”, explica Bruno Juanes, socio líder de Innovación y Manufactura en la consultora Deloitte.
Leer: El potencial de la Industria 4.0 es infinito
El impacto que la tecnología tendrá en el empleo a mediano plazo es innegable, reconoce el especialista, que señala que esto no tiene que ser ni negativo ni positivo. “Habrá tecnología que suponga un cambio en el empleo, como ha ocurrido a lo largo de la historia. A medio y largo plazo sí va a haber un impacto por las diferentes tecnologías, pero en el corto no habrá un apocalipsis robótico”, agrega.
Pero sí es necesario es analizar estos cambios para saber hacia dónde puede avanzar el país.“Empezando por cuál es la situación en México, qué ventajas o desventajas podría tener ante estos nuevos escenarios y cómo deberíamos ir tomando nuestras decisiones de política pública para aprovechar estas ventajas”, señala Víctor Carreón, director adjunto de Planeación y Evaluación del Consejo Nacional de Ciencia y Tecnología (Conacyt).
Leer: Las habilidades correctas para la industria 4.0
Pare el experto, el punto de partida es un sector manufacturero sólido, derivado de la evolución industrial en los últimos 25 años, que ha provocado que las principales exportaciones de México sean productos manufacturados. Pero donde hay que enfocarse es en la generación de capital humano.
“México tiene una capacidad importante para preparar ingenieros en términos de cantidad, donde no hemos hecho todavía el clic necesario es en las áreas donde se van a necesitar o que ya se están necesitando”, reconoce.
Para Carreón, México tiene una ventana de 15 años para generar las capacidades que requerirán los futuros trabajadores antes de sufrir el impacto de los cambios. Por ejemplo, según las proyecciones, pasado este tiempo un robot soldador costará lo mismo que una hora hombre, por lo que, a partir de ese momento, será más barato automatizar que contratar a personas para esa tarea.
Recomendamos: Las tecnologías de la industria 4.0 aumentan 20% la productivida d
Por eso, señala, el trabajo debe iniciar ya, especialmente en áreas como nanotecnología, nuevos materiales o dispositivos médicos, en las que ya hay centros de investigación y en las que México podría posicionarse como potencia media.
“En este momento estamos en la frontera en la generación del conocimiento en dispositivos médicos. Si tenemos las bases sólidas, tendremos capacidad de posicionar a México donde debe estar. No en todas las áreas, porque ningún país tiene eso, lo que hay que hacer es encontrar los nichos”, sostiene el funcionario.
De ahí que, el año pasado, el Conacyt comenzara a diseñar un plan que estará listo el tercer trimestre del 2018, en el que se defina claramente cuál es el objetivo a 25 años: a dónde quiere llegar el país y cuáles son los hitos que se deberían estar cumpliendo cada cinco o seis años para lograrlo.
Leer: Las universidades deben formar profesionales para la industria 4.0
“Si todos los que tenemos que diseñar e implementar política pública hacemos lo mismo, iremos caminando en la dirección correcta. Es importante trabajar de forma coordinada”, asegura Carreón.
Pone como ejemplo la colaboración entre la Secretaría de Energía (Sener), la de Educación Pública (SEP) y el Conacyt para el desarrollo de los Centros Mexicanos de Investigación en Energía (CEMIEs), que agrupa centros de investigación públicos y privados, instituciones de educación superior, empresas y gobierno para trabajar en nuevas tecnologías.
Leer: México debe 'encender' sus motores para entrar a la industria 4.0
Contar con este plan de largo plazo, además, permitirá salvar obstáculos como los cambios de gobierno sexenales y otorgar mayor certidumbre en materia de presupuesto.
En este cambio formativo, la responsabilidad no recae solo en las instituciones educativas públicas o privadas que, poco a poco, aseguran los especialistas consultados, hacen la tarea, también en las empresas. Y muchas han iniciado proyectos para asegurarse talento.
En el caso de ABB, el crecimiento del negocio está provocando que en su Campus de Manufactura de San Luis Potosí la incorporación de personal aumente a doble dígito. La compañía, que cuenta con robots que pueden hacer su propio autodiagnóstico y mantenimiento, posiciona el talento como una de sus mayores preocupaciones.
Recomendamos: Sin talento humano no puede funcionar la industria 4.0
“Es un reto impresionante”, afirma Vicente Magaña, presidente de ABB México. “En San Luis Potosí tenemos siete fábricas y, en la parte de robótica, tenemos un crecimiento de 65% del negocio. Cuando tienes este crecimiento en robótica, no empleas ingenieros y personal técnico de hornos microondas (en esa división)”, explica.
Para asumir este crecimiento, ABB cuenta con un programa de educación dual con la embajada de Suiza (país donde tiene su sede), en el que participan varias universidades y empresas para crear la base tecnológica que se requerirá en los próximos años.
“Estamos invirtiendo en tecnología, pero también en ingenieros”, asegura Magaña, que tiene más de 20 años de experiencia en la industria de la automatización. Este sistema dual se extiende hasta el Colegio Nacional de Educación Profesional Técnica (Conalep), organismo con el que también colabora la compañía.
Leer: La industria 4.0 creó una batalla digital
Un nuevo aprendizaje
Actualizar los planes de estudio y fortalecer la relación entre academia e iniciativa privada será clave para afrontar los nuevos cambios que traerá la tecnología. Pero los avances tecnológicos también ayudarán a tener un mejor talento, asegura Juanes, desde Deloitte.
“Si algo ha demostrado el ser humano, es que sabe adaptarse a los cambios. Y viendo las cosas como una oportunidad, esta tecnología no solo afecta al trabajo, también a la manera que tenemos de aprender nuevas habilidades. El ser humano no solo tiene que cambiar la necesidad de aprender, sino cómo está aprendiendo”, afirma.
Y La tecnología adaptará el entrenamiento de las capacidades, asegura también Luiz Ferezin, director general de la firma de consultoría de servicios tecnológicos Accenture. “El costo de entregar un entrenamiento, al digitalizarse, se empieza a acercar cada vez más a cero. Porque hacer 100 cuesta igual que uno”, sostiene el directivo.
Recomendamos: La SEP y Siemens crearán la asignatura de digitalización e industria 4.0
Esto es especialmente importante a la hora de pensar en cómo capacitar en las nuevas habilidades al personal que actualmente ya está en el mercado laboral y que lo seguirán al menos en las próximas dos décadas.
“A diferencia de otras revoluciones industriales de la historia, hoy el ciclo entre una y otra es menor. Antes no había que pensar en ‘recapacitar’ al personal. Hoy, hay que ajustar los cambios dentro de la misma generación”, detalla Fezerin.
La academia no sólo cambiará sus planes de estudios, sino también su sistema, a fin de que la gente pueda regresar a estudiar varias veces en su vida para aprender nuevas técnicas. La formación dejará de ser un ciclo dentro de las primeras etapas de las personas, para convertirse en un esquema circular al que se estará ingresando de forma continua.
Leer: ¿Cómo avanza la industria 4.0 en el mundo?
De ahí que la responsabilidad recaiga también en cada individuo, que tiene una autorresponsabilidad hacia su formación.
El otro pilar para dar un salto en la formación es la transferencia tecnológica. Carreón reconoce que hoy son pocos los proyectos de investigación que se convierten en un nuevo producto o una mejora en el proceso, muchas patentes se quedan en las instituciones o el CV del investigador.
“Lo que hoy ocurre un poco es que yo, como investigador, tengo mi patente y la pongo en mi cuadrito, pero no salgo a decir que puede hacer tal cosa o aplicarse en tal sector; y estamos a la espera de que el sector empresarial se acerque, pero si no sabe qué tengo, no lo va a hacer”, afirma el funcionario, que agrega que hay una falta de comunicación.
Leer: SEP y Siemens impulsarán la capacitación tecnológica de jóvenes
Invertir en innovación
Esta poca colaboración se refleja también en términos de inversión en desarrollo tecnológico. Del total destinado a investigación y desarrollo en el país, alrededor de 26% corresponde al sector privado. El resto es inversión pública. “Si comparamos estos porcentajes, ya no con los de economías altamente desarrolladas en términos tecnológicos, si no con intermedias con capacidades similares a las nuestras, las proporciones son a la inversa”, asegura Carreón.
El funcionario agrega que en comparación con los países de la OCDE o los BRICS, México ocupa los últimos lugares. En la región, está en la parte alta de la tabla, pero por debajo de Brasil.
Recomendamos: Presentan la iniciativa Nuevo León 4.0
“Tenemos números similares a Colombia y Chile, cuando nuestra capacidad es mayor a la de ellos. No sé si es una falta de interés o que todavía no queda claramente reflejado el potencial que se tendría si se invierte en innovación desde la óptica del sector privado, porque no todo puede ser inversión pública”.
Desde ABB, Magaña coincide que colocar a la innovación en el centro de las decisiones es clave. La empresa invierte aproximadamente 1,500 millones de dólares en I+D. “¿Creemos que es suficiente? Tal vez no, y lo que hemos hecho es generar las alianzas con diferentes compañías para asegurar que podamos tener ese valor para cada uno de nuestros clientes”, explica Magaña.
Este tipo de factores hacen que el primer paso para adaptarse a los cambios no esté solo del lado de la capacitación del talento, sino en el equipo directivo, señala Dante Cortez, líder de vinculación en la iniciativa Nuevo León 4.0, en el que colabora los sectores público y privado para impulsar el desarrollo tecnológico.
Leer: Pasos para convertirse en industria 4.0
“El equipo directivo tiene que sensibilizarse del impacto negativo de no hacer nada, que podría llevar hasta a la muerte a una empresa”, sostiene.
El especialista, que hasta hace pocas semanas era líder de innovación en la regiomontana Frisa y que tiene 20 años de experiencia en la industria, recomienda definir claramente por qué es importante para una compañía la automatización.
“La empresa debe identificar un líder que dirija esta revolución digital, con un perfil de tecnólogo y que vea las oportunidades”, aconseja. Y, una vez identificada el área donde la empresa puede mejorar gracias a la tecnología, desarrollar un equipo que incluya un tecnólogo con experiencia en el área, un ingeniero industrial que pueda traducir a un proyecto esas necesidades y científicos de datos que ayuden en la automatización.
Todos con habilidades blandas que les permitan negociar, ser resilientes, tener empatía y trabajar en equipo.
Leer: México requiere de una política industrial 4.0
¿Trabajo para todos?
El primer robot en manufactura que vio el especialista de Deloitte fue en 1990 y se llamaba Roberto, porque ese era el nombre del trabajador al que sustituyó, cuya jornada consistía en dar vueltas a paquetes de detergente durante ocho horas. “Roberto hizo después trabajos más interesantes. No hay que tener miedo a la fábrica sin trabajadores”, sostiene. Estos cambios permitirán crear trabajos de mayor valor añadido.
Carreón continúa con esta idea a no temer, pero sí ser conscientes de que si no se empieza a trabajar ahora, en 15 años sí podría haber problemas por la automatización. “Existe el riesgo y creo que todos lo tenemos claro. Eso no quiere decir que vaya a haber despidos masivos y que no habrá nuevas oportunidades laborales”.
Recomendamos: La industria 4.0 tiene las ‘alas cortas’
El funcionario pone un ejemplo: cuando México comenzó su apertura comercial, tenía una capacidad portuaria obsoleta. Cuando llegaba un buque de tamaño mediano, la carga y descarga se llevaba a cabo, básicamente, con hombres. Con la instalación de tecnología, el tiempo que tomaban estas maniobras se redujo y también la mano de obra.
“Si antes se requerían 100 hombres, ahora eran cinco: dos para las grúas, dos para las bandas y uno organizando en el patio. Uno podría pensar que se despidieron a 95 personas. Pero lo que ocurre es que con el cambio tecnológico llegan más buques, se necesitan más grúas, más bandas y más gente que las opere, posiciones que antes no existían”, explica.
Leer: México tiene potencial para la industria 4.0
La economía del conocimiento se convierte, más que en una oportunidad, en una necesidad. “Siempre se dice que México ocupa la parte baja del valor de la cadena de manufactura. Somos competitivos porque la mano de obra es barata y hay muchas oportunidades de salir de esa percepción abrazando la economía del conocimiento. México no tiene la opción, tiene el deber de abrazar estos cambios y ponerse a la vanguardia”, afirma Juanes.
El especialista asegura que existe el talento innovador, la capacidad, el flujo de capital, el interés y no hay una razón objetiva por la que no pueda lograrse. Solo es cuestión de coordinación unir toda esta materia prima y ponerse el objetivo de liderar en la economía digital.